May 17, 2024 | Written by: Charlene Yauch, Director of the Center for Quick Response Manufacturing
In recent years, the pace of change in business (and life in general) has accelerated to unprecedented levels. It is clear that success in business now and in the future will require agility. But, just what is agility? And, what policies or techniques can be implemented to help ensure that businesses are agile? What will enable companies to react and proact in ways that move the business forward in our increasingly dynamic world? This article will describe two approaches to defining agility and then identify several ways that the principles of Quick Response Manufacturing (QRM)1 can help your organization become more agile.
What is Agility? – Approach One
Agility is a concept that has been defined in numerous ways, but one relatively common definition is that it is a firm’s ability to adapt continuously to a complex, turbulent and uncertain environment. One approach to agility that I find particularly meaningful is the work of Rick Dove, CEO of Paradigm Shift International and Adjunct Professor at Stevens Institute of Technology. Dove states that any company is technically able to respond to unpredictable change triggers from the external environment, but agile companies are those that respond successfully based on four change-proficiency metrics: cost, time, robustness, and scope2. Cost and time refer to whether the changes are implemented quickly and at reasonable costs. Robustness refers to whether the change was implemented in a manner that produces quality results without the need for constant attention, and scope indicates the magnitude of change that can be accommodated in the future (in other words, has the change expanded the longer-term flexibility of the organization). Since future triggers for change are unpredictable, those manufacturers who employ change strategies that enable scalability, reconfigurability, and reusability are more agile.
What is Agility? – Approach Two
My own approach to agility involves a greater emphasis on the environment of the manufacturing plant3. Manufacturers that are agile are those that achieve success within a dynamic or turbulent environment. The image in Figure 1 shows the manufacturing plant at the center and a variety of entities and forces outside the plant that will potentially create triggers for change within the organization. The more triggers for change that are generated, the more turbulent the environment.
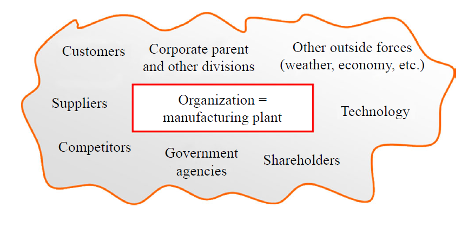
How Can QRM Principles Help Achieve Agility?
In order to improve agility, manufacturers need to excel at responding to unexpected triggers for change. Here are several ways that implementing QRM principles can increase organizational agility.
- Focus on speed and responsiveness with all processes
- In order to develop your company’s agility, it is helpful to have speed as a competitive advantage and to train employees to make time-based rather than cost-based decisions. Make process flow time (or manufacturing critical-path time, MCT) a key performance metric. Use it for all kinds of processes, in both shop floor and office operations, such as designing a product, hiring a new employee, or resolving a quality problem. This will ensure that your employees are conditioned to think about the speed of a process. When agility is needed because of an unexpected trigger for change, emphasis can easily be placed on rapidly accomplishing process changes and adjustments.
- Create small batch flow
- Being responsive on the shop floor and across your supply chains is facilitated by producing in small quantities and delivering just in time. This ensures relatively small quantities of inventory are maintained (raw materials, work in process, or finished goods). If a product redesign is needed or the product demand changes, the company will be in a better position to pivot to the new requirements without having to write off a large quantity of obsolete inventory.
- Manage variability
- QRM was designed for manufacturers in High-Mix, Low-Volume (HMLV) production environments or for those making customized products. Because of that, the principles and tools are designed to help companies manage the inherent variability. For example, operating resources (machines or people) at 75 to 85% utilization ensures that work continues to move quickly through the system. Spare capacity is needed to prevent large backlogs from growing and requiring frequent overtime to catch up. Maintaining spare capacity on resources also enables a company to behave more agilely if there is a sudden surge in demand or change in product mix.
- Cross-train employees
- A flexible workforce will increase your organization’s ability to adapt to changes. If employees have an array of skills, they can be flexibly assigned where they are most needed. If employees are accustomed to learning new things, they are more likely to be flexible and willing to continue learning and adapting along with the organization.
- Empower employees
- The QRM methodology recommends moving away from top-down styles of management and instead empowering employees that work within cell teams (shop floor and office). This type of organizational structure will improve the company’s agility by greatly reducing the need for management approvals and creating a team environment in which decisions are made at the lowest level and ideas are regularly solicited.
Implementing QRM within a manufacturing firm will lead to an organizational culture in which people make time-based decisions, the organizational structure is based on product families and is adaptable as needs change, employees are empowered to make decisions within reasonable boundaries, and it is okay to experiment and try new things. This creates a foundation that makes it easier for the organization to adapt when there are external triggers for change that necessitate new products, procedures, and/or processes.
-
Suri, R. (2010). It’s About Time: The Competitive Advantage of Quick Response Manufacturing, Productivity Press.
-
Dove, R. (1995). Measuring agility: The toll of turmoil. Automotive Design & Production, 107(1):12-14.
-
Yauch, C.A. (2011). Measuring agility as a performance outcome. Journal of Manufacturing Technology Management, 22(3):384-404.