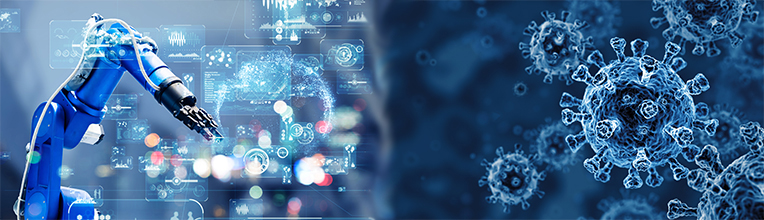
Together we are facing unprecedented challenges. Some of our businesses are shut down due to government mandates. Others must continue because they are essential to the food supply, medical equipment, or our national security. No matter your industry or circumstance you are working on contingency plans. I wanted to share with you my thoughts on key factors for a successful contingency plan:
- Employees—Determine what is needed to keep your employees safe and where possible productively working. Employees are faced with different challenges in their personal lives and with the change in your industry. Treat each employee individually and develop individual backup plans should a specific employee not be able to perform their essential duties.
- Supply chain—Although you may be able to operate “as normal” your supply base may be shut down. How much inventory do you have on hand, on order, in shipment? What will the ramp be once the supply base is back to work? Is your supply base global and how is their regional situation impacting your inventory quantities?
- Priorities—Project plans may be put on hold and new priorities established to meet the needs of your customers. Businesses are being asked to completely pivot to either ramp up production on specific product lines within the portfolio or build new products. With your leadership team, assess your priorities and make sure you are focused on the urgent and important.
- Communication—With so much news on COVID-19, unemployment claims, furlough and wage cut discussions, and the impact to the economy team members are concerned. It is absolutely critical that you communicate to your team(s). As best you can, let them know the plan. Having your team understand your strategy for the crisis will help when we all get back to normal. Communicate often as the world is changing. Daily shift huddles or five-minute standup meetings are more important now than ever to sustain alignment and promote “we’re all in this together.” Leverage different communications technologies including virtual meetings and email to provide your team with direction.
- Equipment—What are the key tooling and equipment to assure daily throughput is achieved. Are team members crossed trained to assure coverage, are maintenance activities being completed, and do the required MRO supplies exist? Assess and identify the most critical equipment and develop an action plan in the event your key equipment is not able to run.
Know you are not in this alone. Companies across the globe are creating and working these plans. Tiger teams are meeting daily as the situation is changing and answering the challenge. Leverage your network and the team at UW-Madison should you want to review your plan or discuss your challenges.
Content contributed by Susan Ottmann, program director—Master of Engineering: Manufacturing Systems Engineering